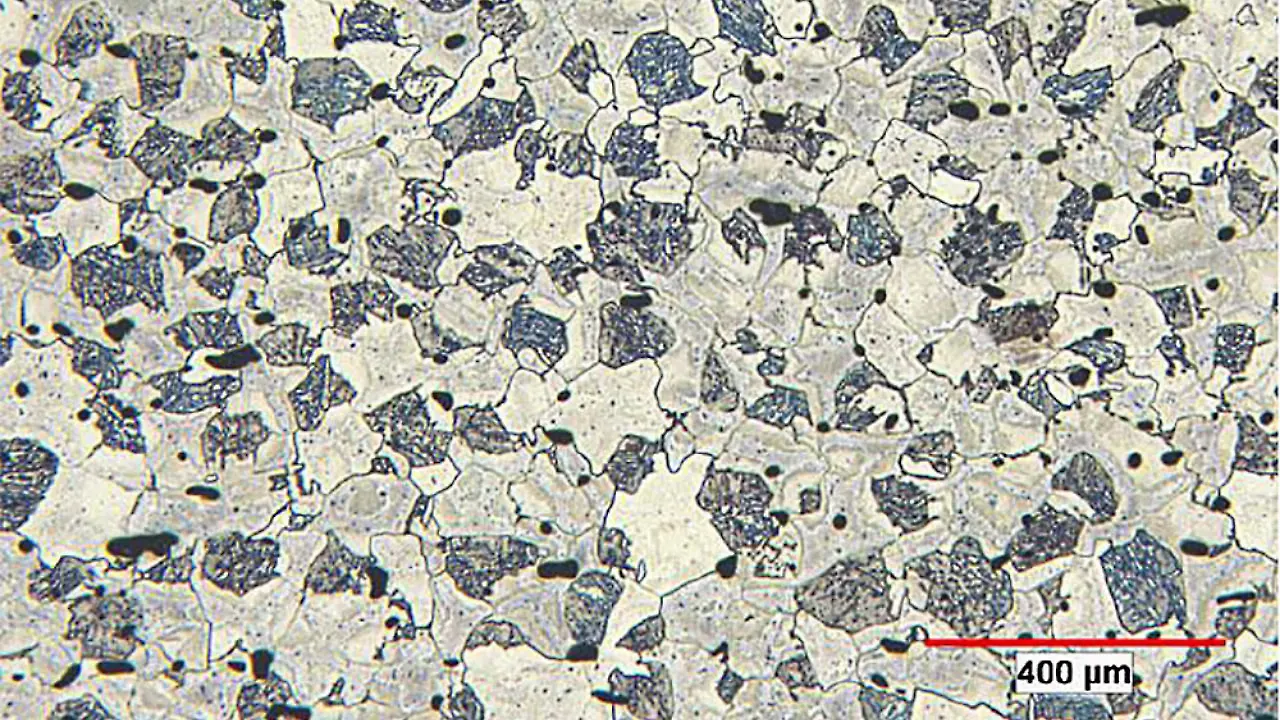
Targeting automotive customers involved in designing sheet metal parts or developing entirely new structural components and manufacturers in the industrial sector, GKN Additive has adapted and enhanced DP600 like material, a widely used low alloy dual-phase steel.
The newly developed metal powder materials DPLA (Dual Phase Low Alloy) and FSLA (Free Sintering Low Alloy) meet similar requirements for mechanical properties as DP600 (HCT600X/C), such as higher ultimate tensile strength (UTS) and low yield strength to UTS ratio. It can be used in laser powder bed fusion and binder jetting processes.
The new powder materials are specialised for additive manufacturing in terms of spreadability, laser absorption and sinterability.
Christopher Schaak, Technology Manager for Binder Jetting at GKN Additive, said the traditional DP600 offers specific standardised mechanical properties achieved by heat treatment. The company's dual-phase steel additive manufacturing materials are flexible in their characteristics, as their mechanical properties can be tuned more widely by the heat treatment after the laser or binder jetting process. This enables various use cases in the industrial sector and makes the material an attractive raw material for a broad spectrum of customers, he added.
New design possibilities
The new material developed helps the users offer new design possibilities, faster functional validation and create a potential for weight reduction.
Using structural components made through additive manufacturing process help in cost optimisation and weight reduction, explained Schaak. For example, for manufacturers in the automotive sector, these two materials offer a new level of design freedom and potential for weight reduction. With these additive manufacturing processes, manufacturers in the automotive industry can construct body parts differently from traditional sheet metal parts. It is also beneficial over tailored blank, sheet-metal parts and support parts that need to be formed and joined together to achieve a specific stiffness.