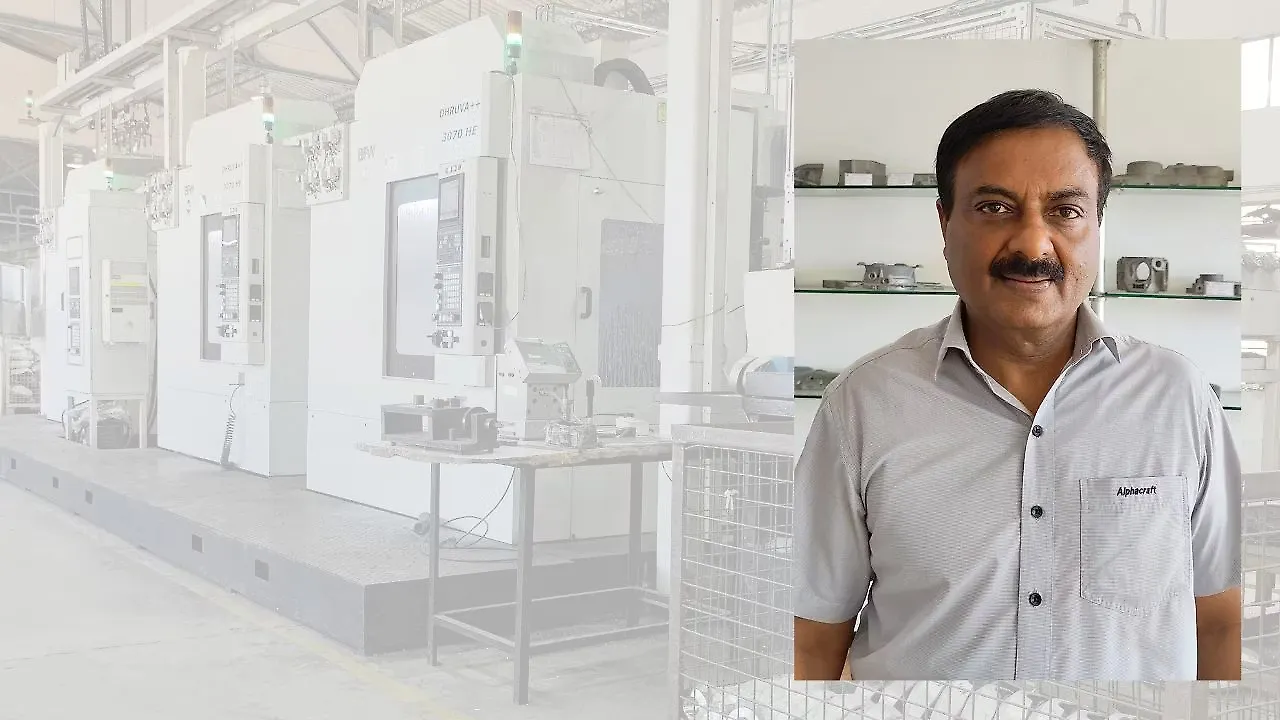
Coimbatore-based Alphacraft is investing nearly INR 80 crore to set up its fifth plant, M Ramesh, Managing Director, told Mobility Outlook.
This has been a result of new orders from the likes of Aston Martin, which wants powertrain parts to be developed for its new sports car. Alphacraft already supplies 16 parts to Aston Martin and is now developing eight more for the next offering.
Additionally, the aluminium die-cast maker will supply two viscous clutch projects for overseas customers. It is also gearing up for orders from some electric carmakers for aluminium battery enclosures.
The other big customer is William Advance Engineering, a leading technology and engineering services business involved in motorsport. Alphacraft is developing large casings for its EV batteries that will be shipped to the US.
It also meets the needs of Mahle Behr and Modine Thermal Systems in the US as well as Porsche in Germany. Other overseas customers are located in Mexico, the Netherlands, the Czech Republic and France.
Back home in India, Alphacraft supplies fork arms to Ola Electric and is now working on the next model. It also caters to Gates India, John Deere and Modine.
The company’s parts basket includes powertrain aggregates, engine cooling systems, viscous clutch, housings and transmission parts.
Ramesh said there were some interesting prospects from three e2W makers in India for aluminium cast products. The company plans to move beyond machined castings to offering a complete system in this new era of mobility options.
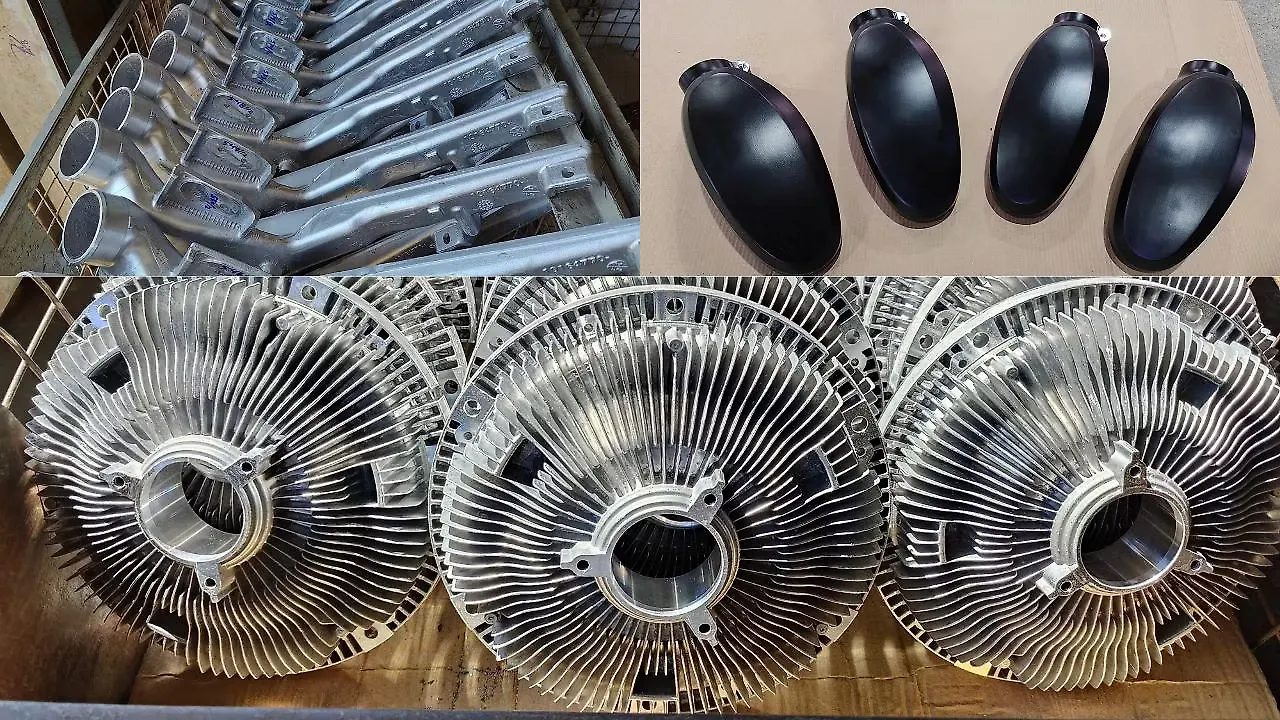
New Facility
The new facility, being readied at the Coimbatore District Small Industries Association Industrial Park, will be commissioned in two phases. First, it will house gravity die-cast (GDC) operations that will move here from the mother plant set up in 1998.
The first phase will have about 50,000 sq ft of space, with an additional 70,000 sq ft coming up in the second. The plant will be up and running in about 18 months and emerge as an IGBC-certified green building with its own effluent treatment plant and technologies to harness daylight while saving on electricity.
The facility will help Alphacraft increase the monthly capacity of GDC from 200 tonne to 500 tonne. Ramesh said the idea is to consolidate the GDC operations under one roof and modernise other plants. The company is also investing in a 2MW solar farm to support producing green castings in the long run.
According to a clearly exasperated Ramesh, the challenge for any entrepreneur is to get all clearances in place from a host of Government departments to run the factory. “The single window clearance reference is merely on paper. In reality, there are over 20 windows where it is akin to building a wall in front of these windows and then creating another window in the wall,” he laughingly added.
Alphacraft was a die maker till 2006 and forayed into castings when it was apparent that it was not optimally reaping the benefits of its technological expertise in dies. As a result, the company gradually expanded into other types of castings manufacturing, such as high and low-pressure die casts, besides growing the capacity of its tools, dies and assembly operations.
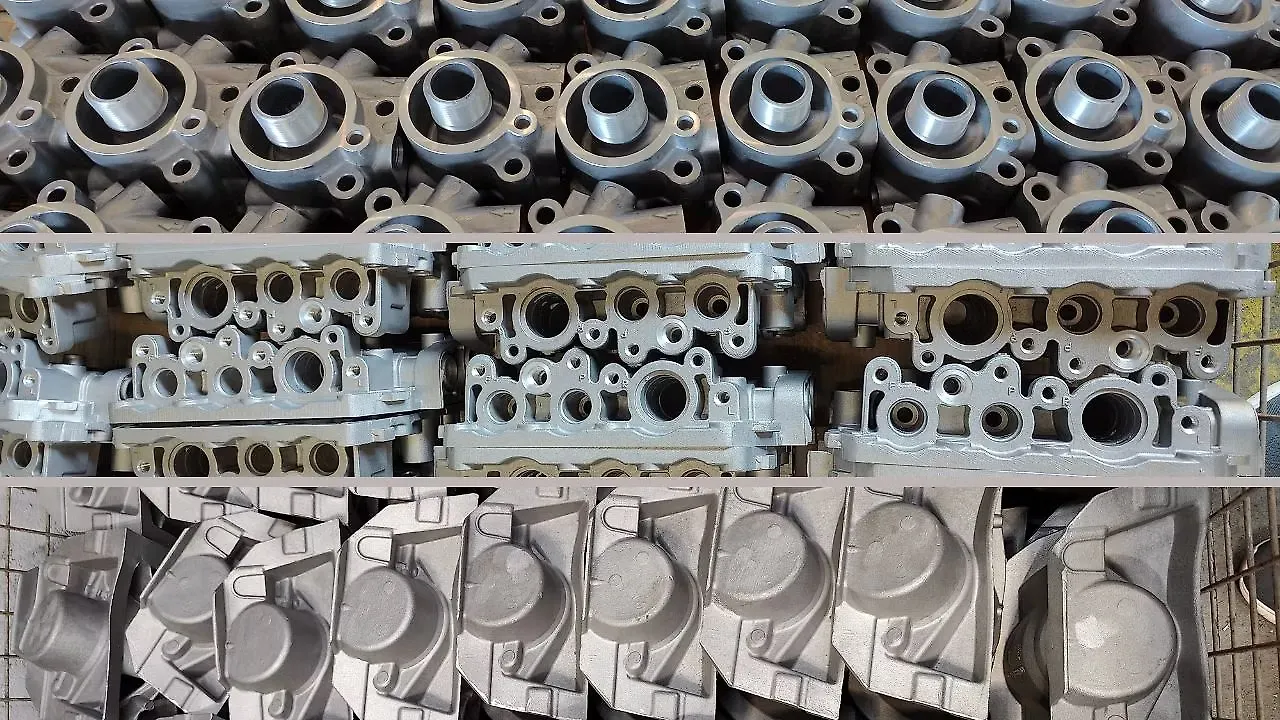
Shifting From China
The focus on GDC stems from making the most of an opportunity available to make parts with this technology. China controls about 90% of the global GDC market, while India’s share is less than 5%. Today, with customers seeking an alternative to China, Alphacraft sees immense potential in supplying GDC parts from India.
GDC’s production cycle time is high and calls for more space and machines. Hence, continued Ramesh, not many companies are keen to take this up as an option. The other challenge emanates from the fact that customers give product designs that are not castable. This could lead to product failures or rejections owing to poor quality and higher costs.
Alphacraft's strength lies in making tools and dies, from where it expanded to making castings from all forms of the manufacturing process. Besides, said Ramesh, its USP lies in offering solutions to customers in designing castings that enhance efficiency/longevity and reduce waste which will keep costs in check.
Alphacraft makes a range of castings from 250 grams to 20 kg. The present capacity of 350 tonnes/month will be doubled in less than three years. The company reported a turnover of INR 100 crore last fiscal and hopes to double this in less than 30 months thanks to this new slew of orders.
Also Read:
Brakes India Creates Benchmark In Supplying Green Castings For Volvo
Ola Leads 2022 E2W Retail Race, Okinawa, Hero Electric Trail
LG Electronics Honours Rane Light Metal Castings America With Best Supplier Quality Award