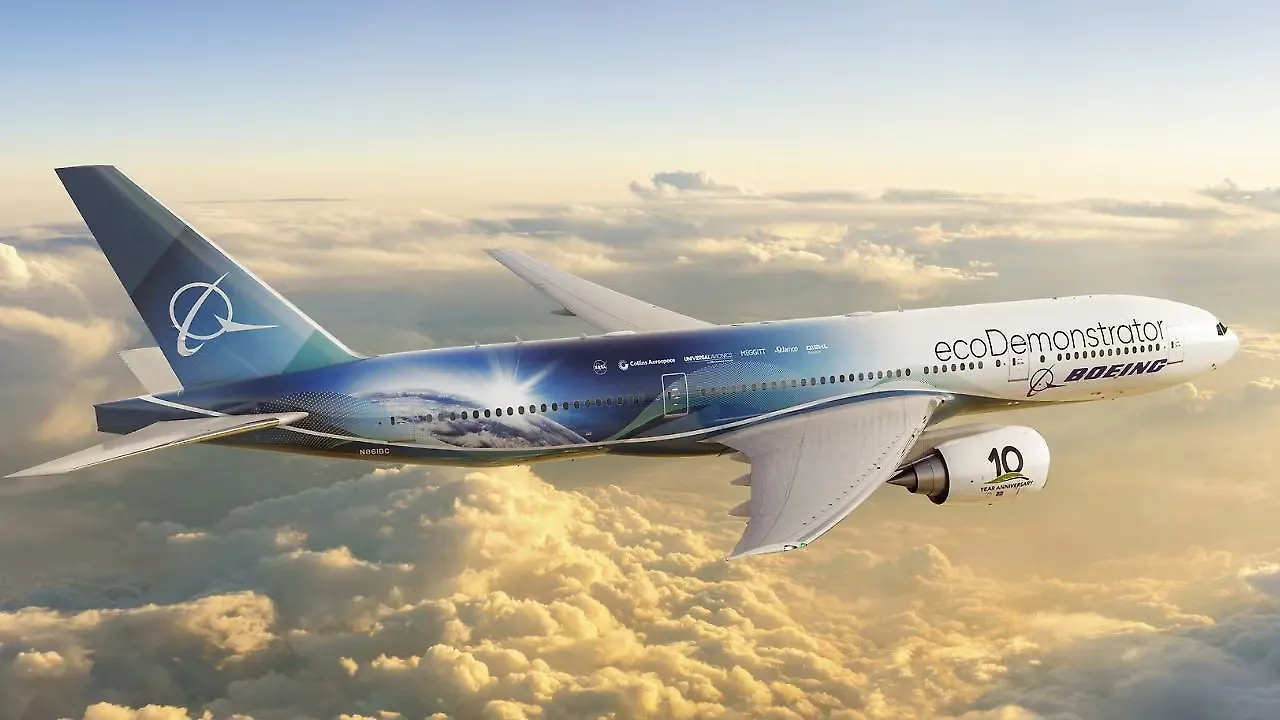
The Boeing ecoDemonstrator Programme, which is underway in its 2022 avatar, has significantly advanced the aviation industry with path-breaking initiatives driving a more sustainable future for aviation.
Boeing launched the ecoDemonstrator programme in 2012 to improve efficiency, minimise the environmental footprint and enhance safety in aviation. Over a decade, the ecoDemonstrator programme has evaluated 230 technologies, including many that have reduced fuel use, emissions and noise, and greater use of sustainable materials. According to Boeing, the continuous testing resulted in a much better understanding of reducing noise emissions from commercial jetliners.
Rae Lutters, EcoDemonstrator Programme Manager, Boeing, said, “Since 2012, we’ve tested more than 200 technologies, and we have found that a third of those technologies have made it into our products and services, and those technologies aid in the reduction of noise, reduction of fuel, cleaner emissions, the safety of the passengers and environmental impacts. Our ecoDemonstrator motto is: Innovate, collaborate and accelerate, and we’ve held to that motto since we started in 2012.”
The ecoDemonstrator programme has delivered several technologies that have transitioned into commercial use on Boeing jetliners. These include the aerodynamically efficient winglets on the 737 MAX, iPad apps that provide real-time weather and other information to pilots, enabling them to improve fuel efficiency and reduce emissions, custom approach path information to lower community noise and flight deck touch-screen displays and a camera system on the 777X that have enhanced flight safety by helping pilots avoid ground obstacles.
Since 2012, the ecoDemonstrator programme has used nine different aircraft types in the B737-800, 737-9 MAX, B787-8 and 787-10, B757, Embraer E170, B777-200, B777 Freighter and the 777-200ER (Extended Range).
Testing Technologies
The 2022 ecoDemonstrator programme commenced in June with Boeing opting to use a company-owned B777-200ER widebody jetliner. Boeing is testing 30 new technologies to improve sustainability and safety for the aerospace industry over six months of flight and ground tests. The 2022 ecoDemonstrator will fly on the highest approved blend of Sustainable Aviation Fuel (SAF) available for all flight tests. Boeing will use a 30/70 blend of SAF and conventional jet fuel throughout the test period on the 777-200ER test aircraft.
In 2021, Boeing launched a multi-year partnership with the National Aeronautics and Space Administration (NASA) to collect and analyse data on SAF emissions. Boeing and NASA have been performing ground testing on engine particles and trace gas emissions with various blends of SAF. This was conducted alongside a demonstration flight with 100% SAF in one engine. The testing took place in October 2021 at Boeing Field in Seattle on that year’s ecoDemonstrator aircraft, an Alaska Airlines 737-MAX 9 powered by CFM International LEAP-1B engines.
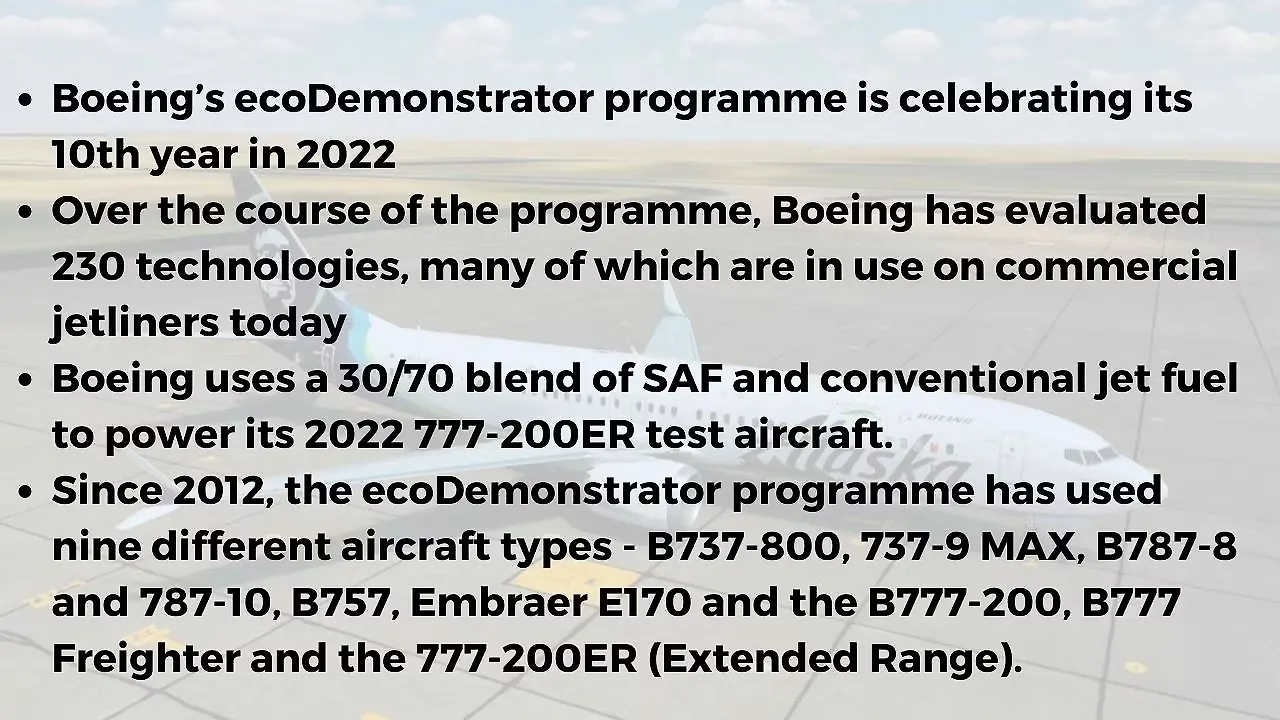
The project's goals were to quantify these engine emissions while burning 100% SAF for the first time and compare the results to those obtained for conventional, petroleum-based Jet A fuel and blends of the SAF with Jet A. The four investigated jet fuels were: 100 % SAF, 50% SAF – 50% Jet A Blend, 30% SAF – 70% Jet A Blend and 100% conventional, petroleum-based Jet A Fuel. Earlier in the ecoDemonstrator programme in 2018, Boeing, in partnership with FedEx Express, conducted the world’s first commercial airliner test flight flown on 100% SAF in both engines.
Among the other technologies being tested this year include SMART vortex generators and small vertical vanes installed on the wing, improving aerodynamic efficiency during take-off and landing. Boeing is collaborating with NASA to test these vortex generators. While these are commonplace in aviation, Boeing and NASA continue their work on SMART vortex generators, which use shape memory alloys developed in collaboration with the latter. These SMART vortex generators can retract into the wing during cruise, improving fuel efficiency and reducing carbon emissions.
Boeing will also trial additively manufactured airplane and engine parts which will be lighter and less complex to manufacture, thus helping reduce fuel use and manufacturing waste. The use of additive manufactured parts on commercial jetliners will have dramatic benefits in the future. Boeing is now testing an additively manufactured Auxiliary Power Unit (APU) exhaust duct support panel and an engine bracket, which will provide significant weight savings and be easier to manufacture. Boeing’s Additive Manufacturing Innovation Center developed the APU exhaust duct support panel and engine bracket.
The ecoDemonstrator pilots also test the next-generation head-worn Head-Up Display (HUD) and an enhanced vision system (EVS) camera. The SkyLens HUD is a transparent screen that places key information directly within a pilot’s line of sight and is being tested by Boeing in partnership with Universal Avionics. The future use of such an enhanced vision system will allow pilots to see in low-visibility conditions, thereby enhancing safety by improving situational awareness. This newly enhanced vision system is also expected to be significantly lighter than existing technologies in this domain.
Boeing has committed to eliminating the use of Halon 1301 (the standard agent for extinguishing airplane fires) across all its commercial airplane models. Due to its ozone-depleting properties, international environmental and aviation regulations have already imposed cut-off dates for using Halon 1301. As a result, the airframer is testing the discharge performance of a new fire suppression agent for the airplane’s cargo compartment in flight, which is being done in partnership with Meggit. The programme is a continuation of the 2021 ecoDemonstrator; also being tested is a new air chiller that uses an environmentally-preferred refrigerant, done in partnership with Collins Aerospace. Such environment-friendly refrigerants could find future use in airplane galleys which contain refrigerators to keep food and beverages cold in flight.
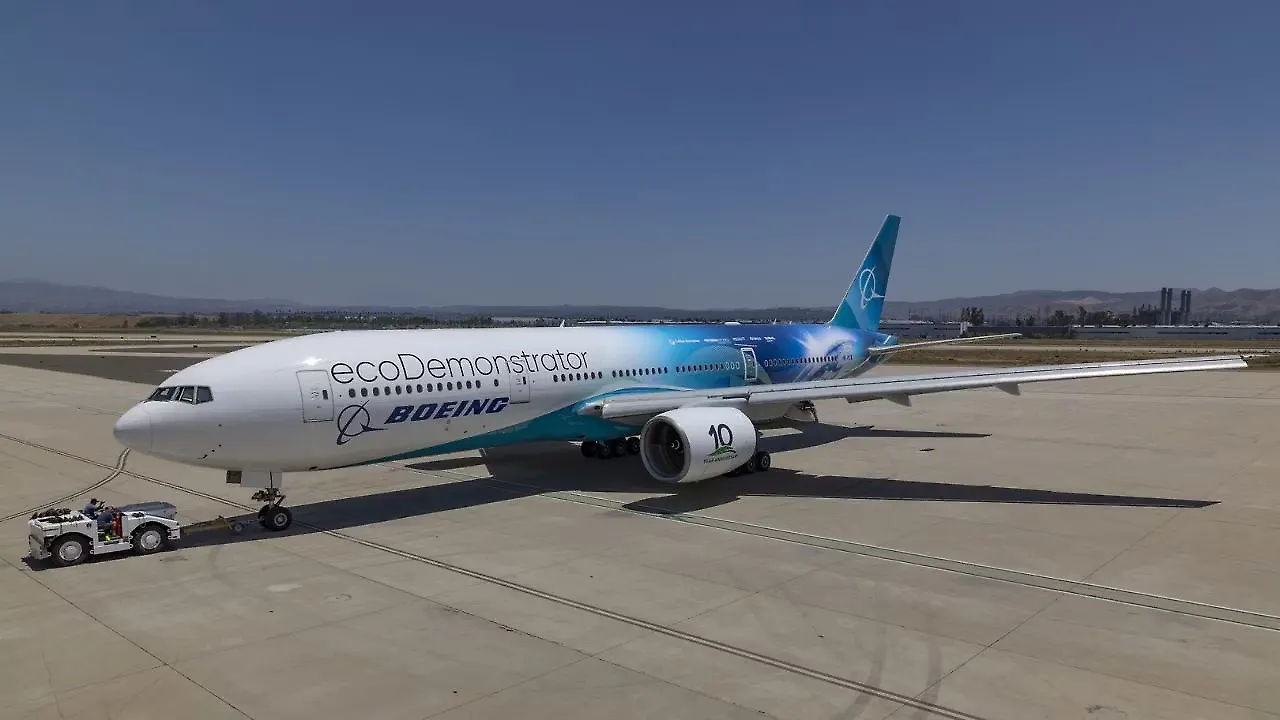
The 2022 ecoDemonstrator programme also tests a water conservation system that uses wastewater from handwashing to flush the lavatories. Boeing is undertaking this work in partnership with Diehl Aviation, which could result in potential weight savings per flight of 181 kg.
Building On Progress
Boeing’s 2021 ecoDemonstrator Programme saw it partner with Alaska Airlines to use its modified 737-9 aircraft. The five-month programme was completed in December 2021 and included participation from Cobham, Inmarsat, Hanwha and AvionX. The 2021 ecoDemonstrator programme was used to flight test about 20 technologies. Following the completion of testing, Boeing was to reconfigure the aircraft for passenger service and deliver the aircraft to the Alaskan carrier by the middle of this year.
The primary focus was testing advanced technologies to reduce aircraft emissions and noise. A new engine nacelle design was evaluated during flight testing, in which the 737-9 demonstrator aircraft’s right engine nacelle was modified with advanced acoustic liners and other treatments made to the thrust reverser. The new engine nacelle was tested with the dual objective of reducing noise emissions from current-generation engines and from next-generation ultra-high bypass engines with compact nacelles. Next-generation ultra-high bypass engines will be shorter and have larger diameter fans than present engines. The testing undertaken in 2021 was meant to generate data to guide the designs for next-generation models.
Boeing also tested a cabin sidewall panel made from recycled carbon composite material left over from the manufacture of wings for its new 777X widebody jetliner. The cabin sidewall panel was subjected to acoustic testing to ensure that it met Boeing’s performance requirements, including noise and weight reduction. The use of carbon fibre material left over from the composite airplane manufacturing process would help reduce waste going to landfills from future airplane designs.
Also Read:
Boeing Unveils Latest ecoDemonstrator, Test Starts This Summer
Boeing Jets To Be Tested With Alder Derived SAF
Boeing Makes Largest-ever Purchase Of Sustainable Aviation Fuel For Commercial Operations