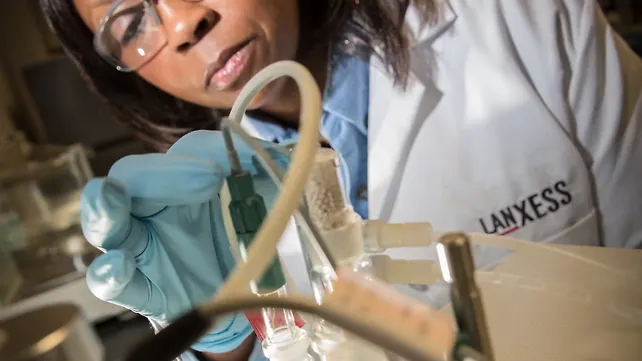
In a bid to demonstrate the technical plastics’ capacity to satisfy the demands of electric vehicle (EV) battery enclosures, Lanxess and Kautex Textron have conducted a comprehensive examination using a jointly developed technology demonstrator made from polyamide 6 (PA6) and reinforced with continuous fibre.
The demonstrator was developed based on the aluminium battery housing of a mid-size electric vehicle and designed for mass production.
It is manufactured in a single-stage compression moulding process with a moulding compound based on the polyamide 6 compound Durethan B24CMH2.0 from Lanxess and does not require any further rework.
Notably, the tests on the technology demonstrator were carried out in accordance with internationally recognised standards for battery-powered electric vehicles, such as ECE R100 from the Economic Commission for Europe or the Chinese standard GB 38031.
During the study, the company was responsible for the material development, and Kautex Textron was for the demonstrator’s engineering, design and manufacturing process.
The large-format all-plastic enclosure, measuring around 1,400 millimetres in length and width, demonstrated its performance in all relevant tests.
The test revealed that it meets the requirements of the mechanical shock test, which is used to examine the component’s behaviour in the event of severe shocks, and of the crush test, which the developers use to examine the resistance of the battery enclosure in the event of slow deformation.
Moreover, the results of the drop and vibration tests were also positive, as were those of the bottom impact test. This test examines the stability of the batteries, which are mostly accommodated in the vehicle floor, in the event of ground contact with the vehicle structure or of impacts from sizeable stones. Presently, an enclosure prototype is being road tested in a test vehicle to verify its suitability for daily use.
Dr Christopher Hoefs, Project Manager e-Powertrain, Lanxess, noted that the near-series demonstrator passes all mechanical and thermal tests that are relevant for such enclosures. Also, solutions for the thermal management and leak tightness of the enclosure, for example, have been developed.
Interestingly, the thermoplastic component design also makes recycling the enclosure easier than thermoset materials such as sheet moulding compounds (SMC).
Dr Hoefs stated that calculations revealed that the carbon footprint of the plastic enclosure is over 40% smaller than an aluminium design. The lower energy use in the production of polyamide 6 compared with metal and other factors – such as the omission of time-consuming cathodic dip painting to prevent corrosion where steel is used – help to minimise the carbon footprint.
Interestingly, technical plastics such as polyamide 6 offer numerous benefits for designing battery enclosures for electric vehicles – in terms of sustainability, manufacturing costs, weight savings and economical, functional integration, for example.
However, there were previously lingering doubts about whether these large and complex components can also meet the very demanding requirements in relation to mechanical strength and flame-retardant properties.
Also Read
Lanxess Joins Advent International For High-Performance Engineering Polymers